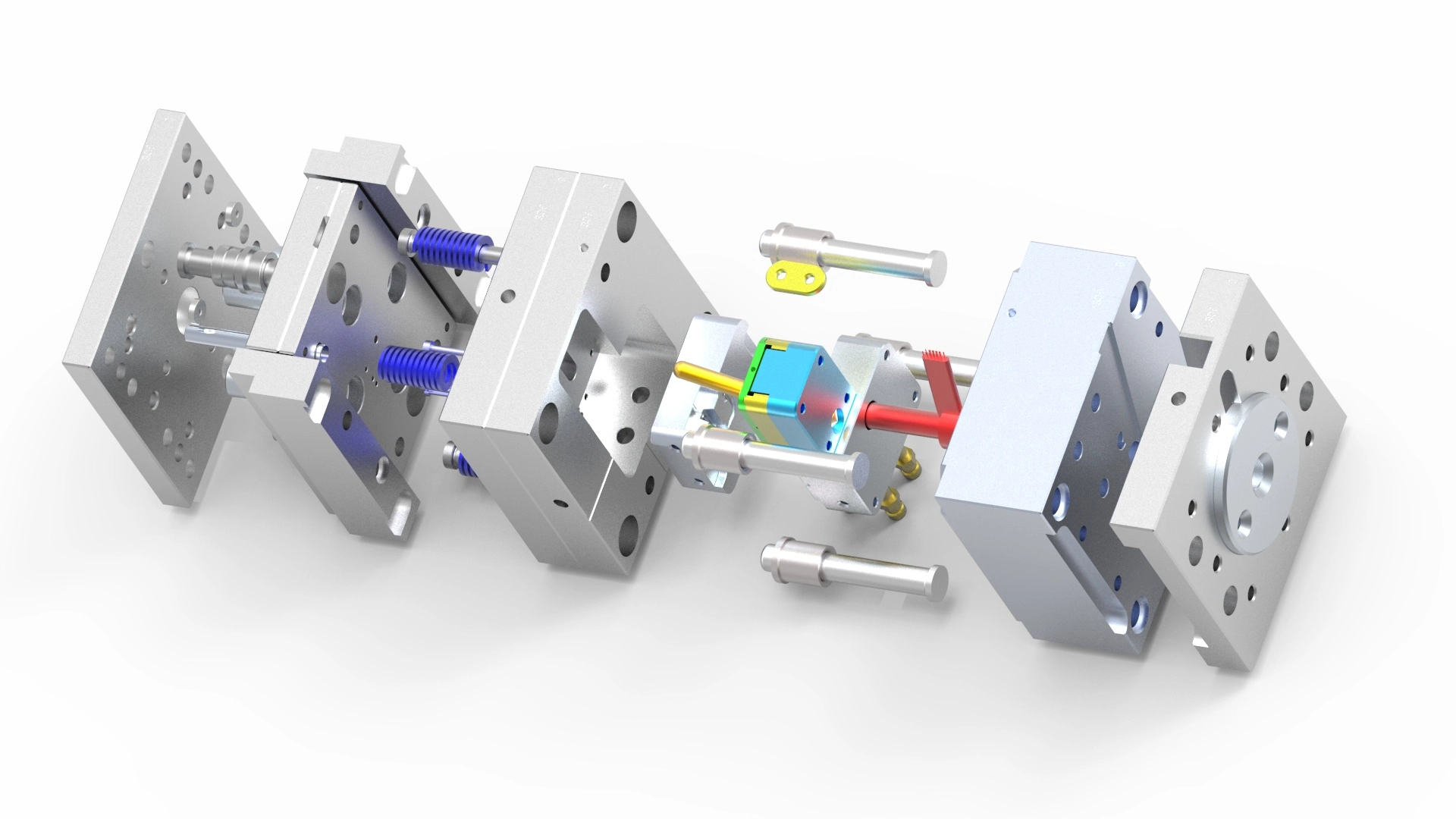
Designing a plastic injection mold is a critical process that directly impacts product quality, production efficiency, and cost-effectiveness. As a professional plastic injection mold manufacturer, Wanjiada combines engineering expertise with practical experience to deliver molds that meet precise client requirements. Below is a step-by-step guide to designing an effective plastic injection mold:
Product Analysis and Requirements
Understand the Part Design: Review the 3D CAD model of the plastic part and identify significant features (e.g., wall thickness, undercuts, ribs, and bosses).
Material Choice: Choose the right plastic resin (e.g., ABS, PP, PC) based on part function, strength, and environmental use.
Surface finish and tolerances: Define the surface texture (e.g., glossy, rough) and the dimensional tolerances to make the end product meet specifications.
Determine the Mold Type and Structure
Mold Type: Decide between a two-plate mold (simpler) or a three-plate plastic injection mold (complex parts with multiple gates).
Cavity Layout: Optimize the number of cavities based on production volume and part geometry. Multi-cavity molds increase efficiency but require precise balancing.
Parting Line (PL): Design the parting line to minimize flash and ensure smooth ejection. The PL location depends on part geometry and aesthetic requirements.
Gate and Runner System Design
Gate Type: Select the optimal gate (e.g., edge gate, submarine gate, hot runner) to control material flow and minimize visible marks.
Runner Layout: Design balanced runners to ensure uniform filling of all cavities. Cold runners are cost-effective, while hot runners reduce waste and cycle time.
Cooling System Design
Cooling Channels: Strategically place cooling channels near high-heat areas to ensure uniform cooling and prevent warping or sink marks.
Material Compatibility: Use corrosion-resistant materials (e.g., beryllium copper) for inserts in high-wear zones.
Ejection System Design
Ejector Pins/Blades: Position ejectors to avoid part deformation and ensure smooth release.
Draft Angles: Incorporate draft angles (1–3°) on vertical walls to facilitate ejection.
Venting and Surface Finish
Vents: Add micro-vents (0.02–0.04mm depth) to prevent air traps and burning defects.
Texture and Polish: Apply surface finishes (e.g., EDM, polishing) to meet aesthetic or functional needs.
Mold Material Selection
Choose durable materials like hardened steel (e.g., P20, H13) for high-volume production or aluminum for prototypes.
Prototyping and Testing
Trial (T0): Test the mold with short shots to validate filling, cooling, and ejection.
Adjustments: Optimize gate size, cooling rates, or venting based on trial results.
Why Choose Wanjiada for Custom Plastic Injection Molds?
At Wanjiada, we specialize in delivering high-performance, cost-effective molds tailored to your unique needs. Our advantages include:
- Expertise: 20+ years of experience in plastic injection mold design for industries like consumer goods, toys, and packaging Industry.
- Advanced Technology: State-of-the-art CNC machining, EDM, and CMM inspection for micron-level precision.
- Rapid Prototyping: Accelerate time-to-market with quick-turnaround prototype molds.
- Cost Optimization: Design molds for longevity (500k+ cycles) while minimizing material waste and cycle time.
- End-to-End Support: From DFM analysis to post-mold services, we ensure seamless production.
Partner with Wanjiada to transform your plastic part concepts into high-quality, mass-produced realities. Contact us today to discuss your project!
Contact Wanjiada
N'hésitez pas à nous appelerwanjiada@gdboost.com
N'hésitez pas à nous contacterWest Of The Dongsizhi Road, Jieyang Airport Economic Zone, Guangdong Province, China